Role of Precision 5-Axis CNC Machining in Automotive Parts Manufacturing
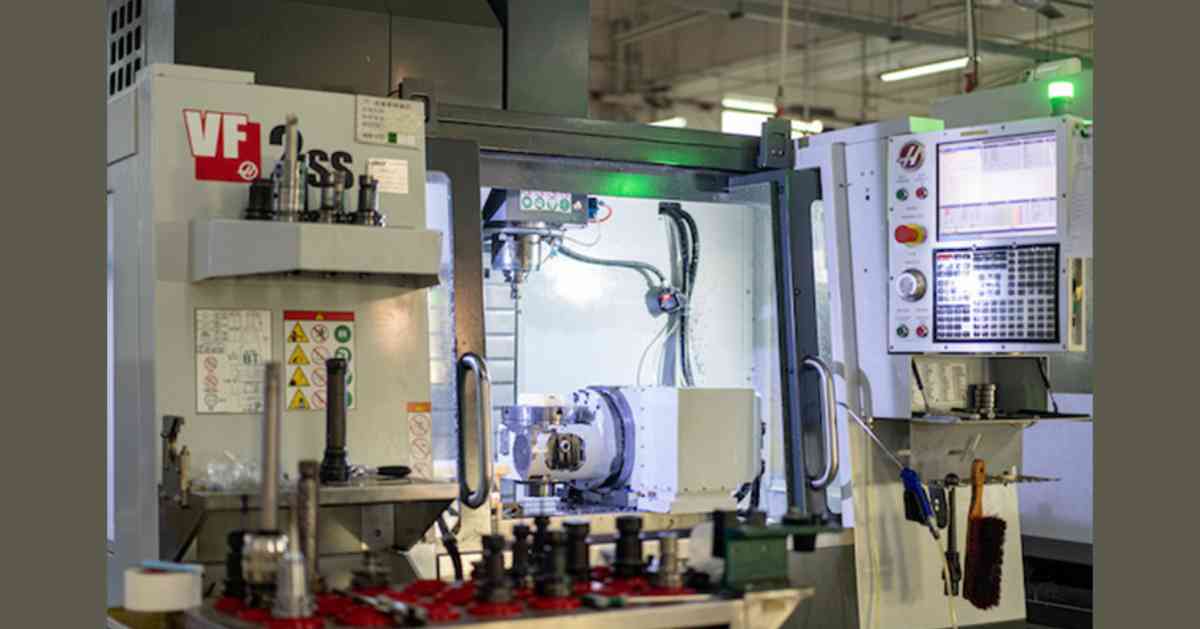
Precision is paramount in automotive parts manufacturing, ensuring optimal performance and safety. Leveraging 5-axis CNC machining technology is integral to achieving accuracy and intricacy across various automotive components such as gearboxes, lighting lamps, suspension parts, and carburetor housings.
The automotive industry heavily relies on 5-axis CNC machining for its efficiency, precision, and ability to streamline production processes, maintaining a competitive edge in the market.
1. Gearbox
Gearboxes, a component in the automotive parts manufacturing sector, stand as the intricate heart of automotive powertrains. Their function demands an excellent interplay with gears and shafts, a feat enabled through superior surface finishes and tighter tolerances integral to automotive parts manufacturing. The use of helical or spiral bevel gears with precisely contoured tooth profiles is made possible through advanced techniques such as 5-axis CNC machining. This process enhances gear meshing characteristics and reduces noise and vibration levels during manufacturing operations.
The machining process of gearboxes using 5-axis CNC machines involves selecting appropriate milling tools, such as gear shapper or hobs, to accommodate the specific hardness and intricacies of the gear design. To choose the appropriate cutting tool, the gear’s pitch, pressure angle, and number of teeth need to match with the cutter.
[Read About: Universal Testing Machines ]
The machining strategy, pivotal to achieving desired gear qualities, incorporates trajectory planning, lineness (defining the spacing and number of tool paths), and cutting strategy, including indexing and cut distribution. This complex orchestration enables the machining of gears with precise geometries and surface qualities.
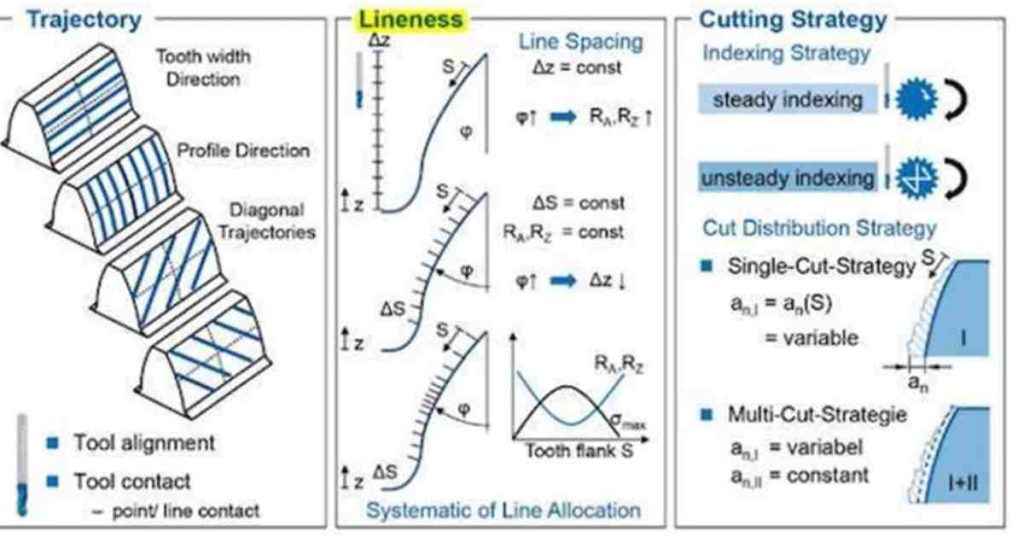
2. Automotive lighting lamps
Manufacturing automobile headlights relies significantly on 5-axis CNC machining to ensure precise production of essential components. Parts such as lens housings, reflectors, and mounting brackets require intricate geometries and tight tolerances to achieve optimal light distribution and aesthetic appeal.
Commonly made from materials like acrylic glass or Poly (methyl methacrylate) (PMMA), these components demand advanced machining techniques to meet design requirements for clarity, light transmission, and structural integrity.
The machining of automotive lighting lamps requires sophisticated techniques to achieve the minimal machining radius of R0.1mm for optical details, with surface tolerances as tight as ±0.02mm and surface roughness post-machining and mirror polishing reaching down to Ra0.1μm and Ra0.02μm, respectively.
5-axis CNC machining enables the creation of optical components with complex geometries and high aspect ratios, essential for thick-walled light guides that ensure perfect light distribution and diffusion. The flexibility and accuracy provided by 5-axis machining help overcome the manufacturing challenges associated with such intricate designs, facilitating the production of lighting effects that meet both functional requirements and aesthetic expectations in automotive lighting systems. This tailored approach underscores the importance of precision machining in automotive parts manufacturing.
3.Suspension parts
Automobile suspension parts, including control arms, strut housings, and steering knuckles, require ultimate precision and accuracy due to their role in vehicle dynamics, ride comfort, and safety.
Achieving precise geometries and tight tolerances with 5-axis CNC machining ensures proper suspension alignment, minimizes vibrations, and enhances overall driving performance.
When it comes to manufacturing these parts, 5-axis CNC machining offers significant advantages over manual methods. In contrast to manual machining, with automated tool changes and uninterrupted machining cycles, CNC machining reduces production lead times, minimizes scrap rates, and enables innovative design solutions tailored to specific vehicle requirements.
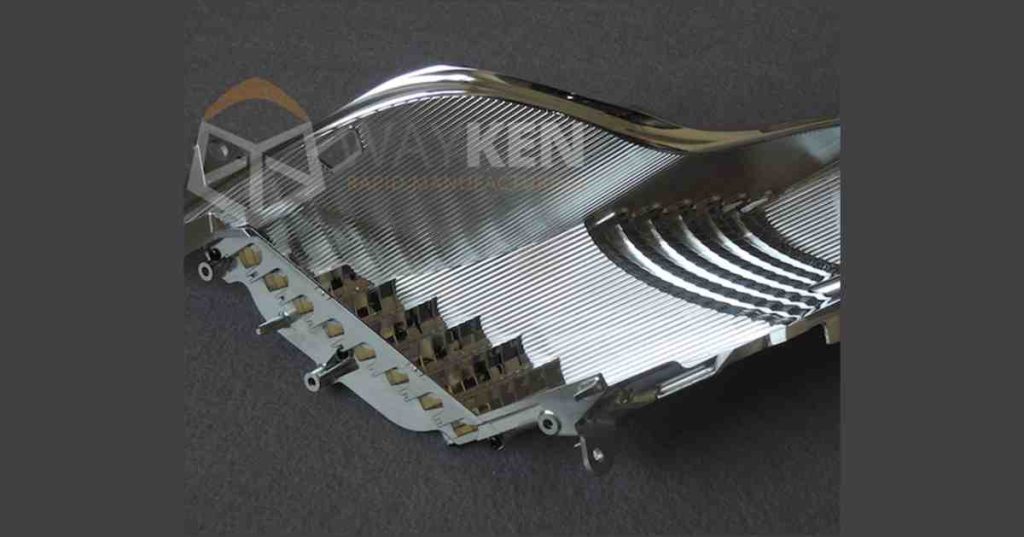
4.Carburetor Housing
Carburetor housings require intricate geometries and tight tolerances to ensure optimal performance and compatibility with the engine system. 5-axis CNC machines excel in machining complex shapes and features, allowing for precise contouring of internal passages, mounting surfaces, and intricate details. This precision ensures proper fuel-air mixture regulation and combustion efficiency, contributing to the engine’s overall performance and fuel economy.
- Throttle Body
The throttle body controls the airflow into the engine by regulating the opening and closing of the throttle plate.
The precision achieved through 5-axis machining ensures smooth operation and precise control of the air-fuel mixture entering the engine. Key to this precision is the meticulous machining of the throttle blade and bore. The throttle blade is manufactured with a 15-degree angle when in the closed position to ensure an optimal seal within the bore, enhancing the engine’s performance by preventing air leaks. This angle, precisely machined on the throttle blade’s outer diameter, complements the bore tolerance of .0012 inches, a specification achieved through the advanced capabilities of 5-axis machining.
- Venturi
The venturi is a constricted section in the carburetor through which air flows, creating a low-pressure area that draws fuel from the carburetor bowl. Precise shaping and dimensions of the venturi help in maintaining proper airflow velocity and fuel atomization.
Through the capabilities of 5-axis CNC machining, manufacturers can achieve the required geometric precision and dimensional stability crucial for the Venturi’s performance. Maintaining a standard tolerance of ±0.001 inch (±0.025 mm) for metals, as specified by ISO 2768-f, is deemed appropriate to balance precision with manufacturing efficiency. This level of precision ensures that the dimensions and shapes of the Venturi are maintained within acceptable limits to facilitate proper functioning.
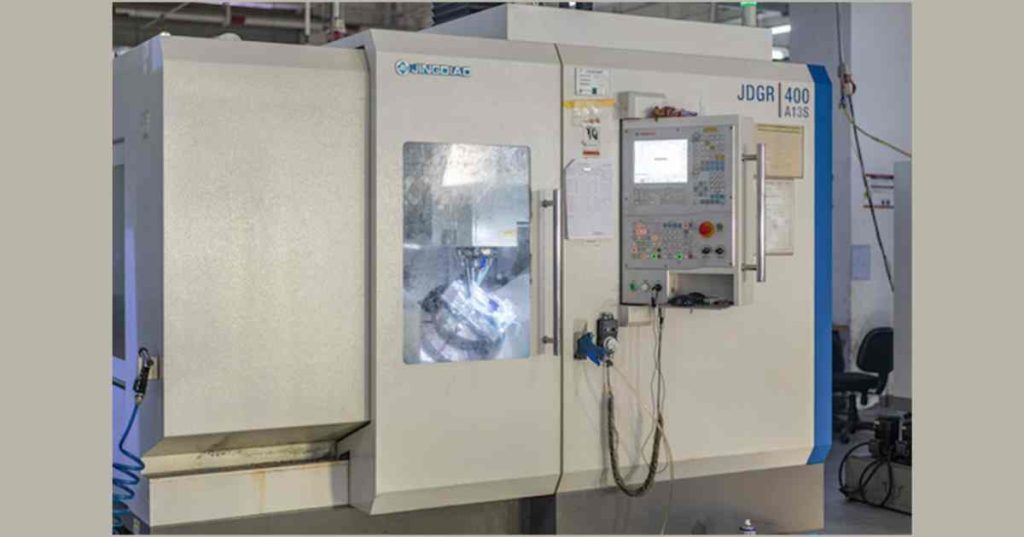
- Float Bowl
The float bowl stores fuel for the carburetor and maintains a constant fuel level. Tight tolerances are required to prevent fuel leaks and ensure consistent fuel delivery to the engine under varying operating conditions. It is typically manufactured from materials like brass or nitrophyl to guarantee durability and efficiency. Ensuring the float level and drop are accurately measured for optimal fuel amounts, as improper settings can lead to rich or lean engine conditions.
- Linkages and Mounting Surfaces
Various linkages and mounting surfaces connect the carburetor to the engine and throttle controls.
5-axis CNC machining of these components ensures proper alignment, smooth operation, and reliable performance of the carburetor assembly.
In automotive parts manufacturing, when mass producing the carburetor, the 5-axis CNC is vital in maintaining precision and accuracy.
It allows production with shorter lead times owing to automated process and tool change, reduced wastage due to multi-axis machining, and high precision and accuracy due to computerized numeric control. Advanced CAM software and real-time tool path optimization algorithms enable tight tolerance control throughout machining.
Conclusion
From gearbox components to automotive lighting lamps, suspension parts, and carburetor housings, 5-axis CNC machining can achieve superior surface finishes, tighter tolerances, and intricate geometries. By leveraging advanced technology and automated processes, automotive manufacturers help achieve vehicles’ optimal performance, safety, and reliability.