Maintenance Strategies: Determining the Right Strategy for Asset Management
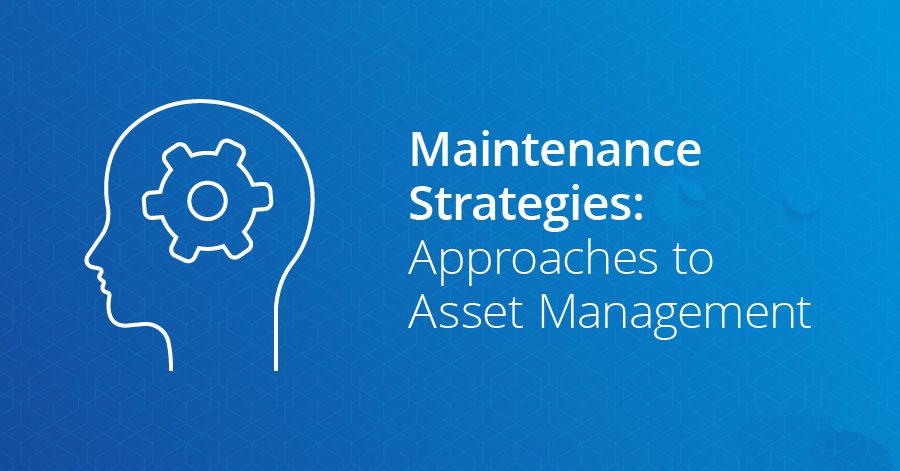
Summary: Applying the correct maintenance strategy that best matches your organization and its asset requires significant consideration. From reactive maintenance to reliability-centered maintenance, here are the pros and cons of each maintenance approach.
To compete at a high level, companies must take a systemized approach to asset management. Without the right maintenance Strategies management system in place, equipment-heavy organizations cannot effectively utilize their assets.
The right maintenance strategy provides facility managers with a holistic overview of their assets in a way that balances service levels, risk, and affordability. But with a host of different maintenance approaches available, certain maintenance strategies work best for different scenarios.
What’s more, there are many different computerized maintenance management systems (CMMS) such as cloud-based asset management software to choose from.
Evaluating the options available can be a difficult task. An assessment of the organization’s assets and size, its financial capability, as well as the experience of the maintenance team must be carried out to determine the right asset management strategy to employ.
Failure to properly account for these factors can lead to poor implementation and integration with existing legacy systems. Choosing the wrong maintenance strategy may also lead to a lack of adoption among users, which can result in project failure.
To help your organization choose the right approach to asset management, we examine the four most common strategies below, highlighting their specific advantages and disadvantages.
1.Reactive maintenance
As the name implies, a reactive maintenance strategy only repairs assets after failure is observed. Also referred to as breakdown maintenance, this reactionary approach means that poor performance or breakdown must first occur before a maintenance procedure can be performed.
Because maintenance procedures aren’t carried out until initiated by some sort of failure, reactive maintenance has the lowest initial cost. There is also no need for maintenance planning as repairs are performed only when the equipment fails.
Certain assets that are considered non-critical such as lightbulbs can benefit from reactive maintenance. Because the asset is low-priority, inexpensive, and poses little to no safety risk, a reactive approach can be advantageous.
Unplanned repairs of redundant assets should account for less than 20 percent of maintenance done within a facility. Devoting any more maintenance time to reactively managing assets can result in huge delays, particularly if the required spare parts are unavailable.
2.Preventive maintenance
Preventive maintenance is a more systematic approach to asset management than reactive maintenance. This type of maintenance strategy maintains equipment in a satisfactory operational condition.
Unlike reactive maintenance which allows the equipment to run to failure and results in unplanned servicing, preventive maintenance inspects and corrects defaults before failure. This approach minimizes asset failure, reducing unplanned downtimes while prolonging an asset’s life cycle.
Preventive maintenance is suitable for assets and equipment that have a critical operational function. Examples of facility equipment that benefit from preventive maintenance include HVAC and electrical systems as a breakdown of these systems can result in a stop in production.
For a majority of assets, preventive maintenance can be implemented through a time-based or usage-based approach.
A time-based approach is a periodic work order that is performed on a set schedule (for example, replacing or cleaning HVAC’s air filter every three months). Usage-based maintenance tracks the usage and operating hours of facility equipment. An example could be a transport truck that needs servicing every 10,000km.
To ensure that preventive maintenance tasks are done according to their schedule, CMMS software and digital technology like an asset management mobile app will be necessary. CMMS software can automatically trigger when a work order must be completed according to preset parameters.
Considerable investment in both time and resources is required to maintain preventive maintenance practices.
3. Predictive maintenance
Despite predictive maintenance being similar to preventive maintenance in that both are scheduled maintenance practices, their approach to increasing the reliability of assets and maintaining satisfactory operational conditions differs.
Preventive maintenance is regularly scheduled and is triggered by time or usage of equipment.
Predictive maintenance, while also scheduled, is triggered by the asset’s condition. Rather than using expected life cycle statistics, as is the case with preventive maintenance, repairs under a predictive approach are determined by the actual condition of the asset.
Because this condition-based maintenance strategy applies corrective action at the optimal time, overhead costs such as labor and material are reduced.
However, implementing a predictive maintenance system requires higher upfront costs when compared to preventive maintenance. Significant expertise and training are also required, as the flow of data and information must be correctly analyzed to maintain predictive maintenance practices.
4.Reliability-centered maintenance
Reliability-centered maintenance (RCM) takes the learnings from both preventive and predictive maintenance to drive significant improvements in asset function, reliability, and performance.
Rather than taking a schedule- or condition-based approach, reliability-centered maintenance identifies failure modes and their corresponding consequences for high-value assets in the organization, developing individualized maintenance schedules to offer greater asset reliability at the lowest cost.
The goal of reliability-centered maintenance is to preserve system functions by determining what systematic tasks can be performed proactively, using cost-effective maintenance techniques.
This is a highly involved process that requires a considerable assessment based on the technical standards set forth by the Society of Automotive Engineers (SAE).
Before a maintenance strategy can be considered RCM-compliant, the following questions must be reviewed:
- What is the item supposed to do and what are its associated performance standards?
- In what ways can it fail to provide the required functions?
- What are the events that cause each failure?
- What happens when each failure occurs?
- In what way does each failure matter?
- What systematic tasks can be performed proactively to prevent or diminish the consequences of the failure?
- What must be done if a suitable preventive task cannot be found?
Answering these questions will help identify how to build a better cost-efficient ratio of available assets.
While reliability-centered maintenance is a very cost-effective approach, in the long run, it has a costly upfront cost. New training formats, as well as maintenance practices, will need to be introduced to shift the mindset towards asset reliability rather than asset functionality.
For many facilities, reliability-centered maintenance is too complex and costly to implement. Only large enterprise-level organizations with experienced maintenance teams may have the resources and investments to properly implement an effective RCM strategy.
Which maintenance strategy is right for your organization?
When it comes to developing a cost-effective maintenance strategy, many organizations will find that there is no one-size-fits-all solution. Each of the strategies listed above has its role in ensuring assets operate in optimal conditions to maintain production efficiency.
While preventive maintenance is the most popular asset management strategy, implementing a multifaceted maintenance strategy approach will enable organizations to maintain optimal asset availability at a sustainable cost.
Once a strategy has been established, organizations must perform ongoing analysis to monitor its effectiveness. This will ensure the new strategy continues to maintain optimal equipment performance.
AUTHOR BIO
Andrew Piechowiak is the General Manager – Asset Management Business at SGE Group International, a multidisciplinary group of companies with core business interests in Asset Lifecycle Management, Land Development, and Software. Aladdin is SGE’s proprietary Asset Lifecycle Management software, designed to empower FM, Maintenance, and Asset teams across multiple industry sectors.