Overmolding V/S Insert Molding – Which One Is Better?
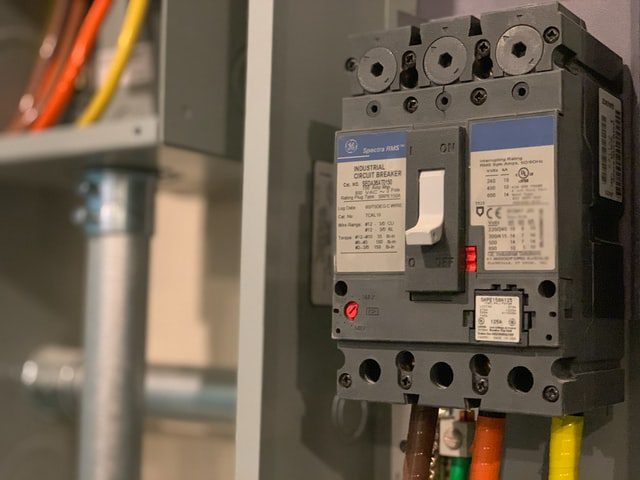
Many individuals evaluate the distinctions between plastic injection molding processes to identify which technique is best for their business. Overmolding and insert molding are two of the most well-studied procedures. Multi-material injection molding part design is frequently used by manufacturers to create items that satisfy a variety of practical and aesthetic functions.
Overmolding and insert molding are two subcategories of the injection molding manufacturing method. The two mechanisms are commonly confused since they have some resemblance, but there are several massive distinctions. These two groups all involve inserting plastic resin into a mold cavity, but the one key difference that many people overlook: all over-molding is insert molding, but not conversely.
It might be debatable at times whether these two methods are preferred. These two plastic injection molding methods are remarkably similar in many aspects. When making such a significant decision, it is critical to grasp the distinctions.
Manufacturers frequently investigate the differences between over-molding and insert molding. To minimize speed to market, the crucial role in this process should be the optimized design stage. The part’s fabrication will also benefit from an improved design.
Let us jump in
Overmolding is a method of combining different materials into a singular service or component in a consistent way. It usually consists of stiff plastic base material with a flexible, malleable thermoplastic outer coating or other comparable materials layered on top.
Overmolding is exceptional in that it brings benefits in a variety of ways while simultaneously lowering overhead expenses. For fragile, minimal electrical gear, the Low-Pressure Molding Process (LPM) is an excellent overmolding electronics approach.
Insert molding is a technique for adding metal pieces to injection molded parts while they are still in the mold, rather than after they have cured, reducing post-molding production and assembly processes. Insert mold is manually or mechanically put on mold cores that are cast into the molds.
Plastic pieces are polymerized in the injector barrels and injected into the mold once the mold halves are sealed, the plastic material streaming around the entrapped inserts. The components are released from the mold once the plastic has hardened, with the inserts now encased in the parts.
The overmolding process of adding another layer of plastic or elastomer fabric to an existing metal or plastic object is also known as insert molding. The metal or plastic item is also inserted into a single-shot injection mold, and an overmold substance is inserted around it.
Advantages of Overmolding
- Overmolding is a very versatile technique. Hand tools, brushes, and blades, for example, may have overmolded arms for enhanced gripping.
- To improve product lifespan, a sensory, smooth, non-slip grip was included to avoid equipment drops while also acting as an ecological buffer to heat, tremor, and noise.
- Aesthetically attractive materials and customized color palettes boost the market appeal and give you a competitive edge.
- The number of needed production stages and related expenses are reduced.
Advantages of Inset Molding
- Additional assembly activities such as click fits, glue, and the use of bolts or fasteners are no longer necessary.
- By enabling the incorporation of crucial metal pieces, design aspects not achievable with plastic alone may be included.
- It’s useful for a wide variety of tasks, including connectors, knobs with threaded fasteners, as well as more sophisticated electronic systems.
- It reduces human error, increases efficiency, and guarantees that cycle durations are as short as possible.
Some common benefits
- Insert molding and overmolding are two types of multi-material injection molding that are comparable yet unique.
- Lower Cost
- Lower Part Weight
- Smaller Part Size
- Faster Development Cycle
- More Repeatable Process
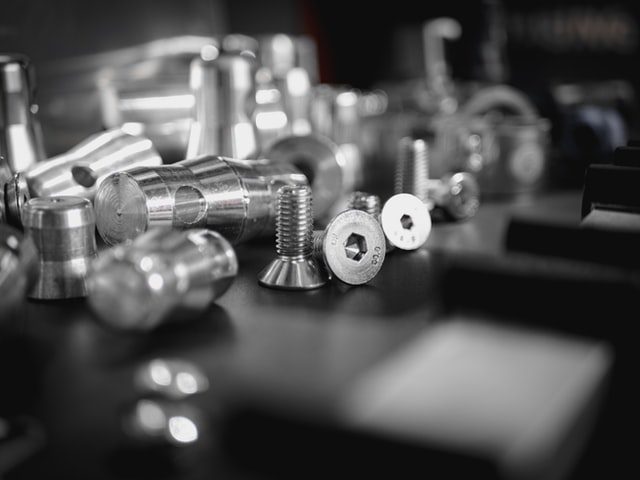
Applications of Overmolding
To ensure component tolerances and tooling dependability, proper mold engineering and implementation, as well as material selection, are critical in bespoke polymer overmolding. In the plastic overmolding procedure, robotic automation is used to position inserts quickly and precisely.
Carefully built bespoke over-molded plastic items can remove the need for a range of secondary procedures such as ultrasonic welding, gluing, gasketing, and assembling, saving the time either retooling current products or inventing new ones.
Medical tools and gadgets, handles with a gentle grip, appliance knobs, controls, and assembly, electronic gadgets and electrical components encased, and window casings with moldings are more applications of overmolding.
Applications of Insert Molding
Metal plugs for insert molding are made using insertion injection materials and are utilized in a variety of sectors, including aviation, healthcare, defense, semiconductors, automotive, and consumer’s markets.
The injection molder’s expenses will be cut because there will no longer be a full-time worker at the equipment. Lower operating expenses can subsequently be passed on to customers.
Screws, filters with fine mesh inserts, studs, vacuum hose connectors, contacts, automobile air ducts, clips, heavy equipment components, spring contacts, medical syringes, pins, surface mount pads are just a few real-time applications.
Some additional information
Overmolding is a difficult task, especially given the numerous factors at play and the risk of repeating errors in thousands of injection-molded duplicates. Overmolding companies should be included early in the part design phase since their knowledge of the different procedures may assist the numerous traps that are ready and waiting to derail the realization of a successful component.
A few general guidelines apply when engineering for overmolded parts: Overmold edges must not feather; instead, they should finish suddenly and at full width against a curb or depression. The over-molds surface roughness can significantly help in the part’s removal from the mold.
It also creates the idea that the object is softer, concealing any defects in the molding process. Door and exhaust design must be carefully considered by mold designers.
The Parting Words
The debate of which one is better is an endless one because there is no definite conclusion to it. Both have their own merits that depend on the usage. It is not a fight that one is above the other. Your house or industry needs a blend of both overmolding and insert molding. The profitable task to do is make use of both accordingly.